
QR code & NFC tag for efficient machine maintenance | 2 supporting technologies
QR code and NFC tag for efficient machine maintenance.
2 supporting technologies
Introduction: Find out how QR codes & NFC tags are revolutionizing machine maintenance and helping technical specialists on the store floor to solve problems in seconds.
Reading time: approx. 4 minutes
Interesting for: Service management, maintenance, after sales, plant and machine manufacturers, field services, industrial manufacturing companies
I. How QR codes and NFC tags on machines and systems make everyday life easier for technical specialists
With these two technologies, you can offer technicians on the store floor quick and easy access to important information directly at the machine.
Quick help with stored service pages
Instead of searching for manuals or instructions, the technician scans the QR code or approaches the NFC tag and gets immediate access to all relevant data, e.g. on set-up service pages. Stored instructions, videos, required tools and materials, storage locations and a direct line to an expert via service chat, call or video call (visual support/remote maintenance).
What is a QR code?
What is an NFC tag?
The QR code already has it in its name QR = Quick Response. The two-dimensional code consisting of a matrix of white and black squares or dots was developed by the company Denso in 1994 and is probably more familiar to most people. Here is an example from us:
Most people are probably familiar with the NFC tag (near field communication) from contactless payment. The tag has been around since around 2002. With an NFC tag, the person simply walks past the microchip and information is transmitted to the NFC-enabled device. The NFC tag consists of a tiny microchip, an antenna and a carrier (usually plastic, so that the tag can be attached).
For example. NFC tags can also be square or already “packaged” in a sleeve, e.g. to hang on a bunch of keys
Service pages, the quick help in case of service
For special inquiries, the specialist enters a search term on the service page in the search window or leaves the search term via voice control (AI - Speech to Text) and finds the help they need on the service page.
Error messages can also be displayed on the service page. One click is all it takes to get direct help with rectifying the problem (e.g. in the event of a recurring problem or maintenance). You can find out more about service pages on our "Documentation HUB" page
This not only saves time, but also reduces the error rate, as specialists can work with up-to-date and accurate information. The ease of use of QR codes and NFC tags means that even less experienced staff can quickly access the knowledge they need, learn and work efficiently.
NFC tags are particularly suitable for concealing them inconspicuously on machines (e.g. if you want to protect your sensitive machine data in particular because frequent visitors come to the factory halls (factory tours / inspections). Your employees know where an NFC tag is located on machines, they read it with their preferred hardware and receive all the information - just like a QR code, only more inconspicuous.
Image description: It's that simple. Scan the QR code or NFC tag with a smartphone, for example, and call up the machine's service page to obtain all the important information.
II Direct access to service pages and visual support
Wherever the link behind the QR code or NFC tag leads - at best, it makes life easier for the specialist on site. One major advantage is direct access to a service page specifically tailored to the machine in question. These not only provide detailed instructions and repair information, but also enable a direct connection to a service technician.
Possible content:
- Instructions and 3D models
- Digital machine files
- Product descriptions
- Images and video instructions, with standard instructions as well as recurring instructions
- Maintenance plans
- Information on spare parts, including markings and stock numbers & spare parts management. This makes it easier to order spare parts and ensures that the right parts are available quickly, which in turn reduces machine downtime.
...and adirect "line" to support. By integrating Visual Support, technicians can communicate live on site with the manufacturer's machine experts, which speeds up problem solving and minimizes machine downtime.
Image description: Example of a simplified service page for mechanical engineering or robotics. It contains useful information for efficient machine repair. With step-by-step instructions, videos, CAD drawings, materials required for the repair, storage locations, stock, ordering processes and, most importantly, immediate contact with the machine manufacturer and its repair experts via service chat, visual support video call and telephone (hotline).
III Machine sales including digital machine file
By using the Documentation HUB within the bitnamic CONNECT software, companies are able to create comprehensive service pages with the content of the respective product (machine or system, etc.) in no time at all. Our customer Amazone has impressively demonstrated how the documentation of its individual agricultural machines can be used for service pages and has in turn been offering its customers direct access to valuable information for years.
IV. Future prospects for QR code and NFC tag technology in machine maintenance
Content behind the two technologies (QR & NFC) continues to evolve, such as access to maintenance histories, spare parts information and the direct spare parts ordering process.
NFC tags can enable more complex interactions, such as automatically triggering maintenance logs or sending notifications to maintenance teams.
The IoT (Internet of Things) opens up new possibilities for both technologies. Machine statuses can already be monitored in real time and service pages automatically updated based on the current requirements and statuses of the machines. Acceptance of the technologies is increasing and the user experience and functionalities are improving. Interaction options are also becoming increasingly complex.
V. Advantages of using QR codes for companies
They help to increase efficiency and productivity by shortening maintenance and repair times and thus increasing machine availability. In addition, companies can reduce training costs by using the technologies, as technicians can learn faster and work more independently thanks to the digital instructions and direct support. Overall, this leads to a reduction in operating costs and an increase in competitiveness.
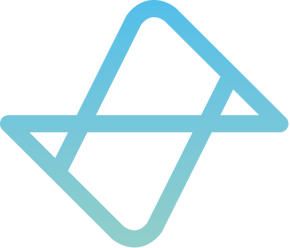