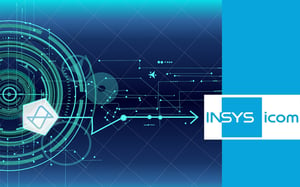
Predictive remote maintenance with INSYS icom and bitnamic CONNECT
Increasingly complex machines, worldwide locations, costs and competitive pressure - these are just a few of the challenges machine builders / operators face. Customer requirements have to be met as quickly as possible, but there is often a lack of time and (qualified) personnel for 24-hour support. The solution: digitalization and remote maintenance. The collaboration between INSYS icom and Bitnamic offers both.
INSYS icom provides the hardware, Bitnamic the software
The company INSYS icom from Regensburg, Bavaria is a digitization expert for industrial data communication. With the help of specially developed hardware, especially industrial routers and gateways, production plants and machines can be easily linked. In this way, systems or other devices can be reached remotely and operating data can be transmitted. Remote maintenance, remote control, status monitoring and networking of data form the cornerstones of INSYS icom and thus connect OT with IT.
As soon as a system has been equipped with a router from INSYS icom and connectivity has been established, Bitnamic comes into play: Our Remote Maintenance software solution - the main component of the bitnamic CONNECT smart service app - allows the service technician on site and an external expert to be connected in the form of a live video transmission, for example, in the event of a problem. The WLAN connection for smartphones, data glasses or other end devices that are compatible with bitnamic CONNECT is enabled by the INSYS icom router.
Advantages of complementary technologies
The combination of the now networked system and remote maintenance access via bitnamic CONNECT offers a multitude of opportunities for machine builders / operators:
- Fast response times and optimization of service calls.
- Real-time data from the machine are made accessible to the user of bitnamic CONNECT via the INSYS icom gateway and thus provide an additional picture of the overall situation.
- The external expert has direct access to the data of the defective system on site.
- Predictive maintenance: When does the machine need service, when does a wear part break? Thanks to predictive remote maintenance, potential incidents can be avoided in advance.
INSYS icom and Bitnamic enable secure, immediate worldwide access to machines, which makes long journeys by experts - and the associated time and high travel costs - obsolete.
The cooperation between INSYS icom and Bitnamic does not only offer the opportunity to save money. To increase efficiency and thus increase sales, it is advisable to integrate remote systems into an (industrial) Internet of Things (IoT / IIot). This allows additional value, for example through data-based process optimization.
Test bitnamic CONNECT without obligation
Digitalization has become indispensable in the mechanical engineering sector; those who want to remain competitive cannot avoid jumping on the Industry 4.0 bandwagon. Bitnamic would be happy to assist you: Experience live the possibilities and additional value for your service, free of charge and without obligation. Simply request your preferred demo appointment.
You can find more information about the INSYS icom solutions on the website: www.insys-icom.com.
If you have any further questions about the topic of system networking and connectivity, as well as operating data acquisition, INSYS icom is at your disposal:
Contact:
Kristian Haizmann
Business Development Manager
T: +49 941 58692-476
M: +49 171 2978868
khaizmann@insys-icom.de
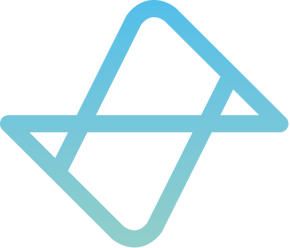